What is Inventory Management? Benefits, Types, & Techniques
Inventory management is the process of monitoring, managing and forecasting the quantity and type of items that are in stock. It is a key component of business strategy, as it allows businesses to optimize their production and reduce or eliminate waste.
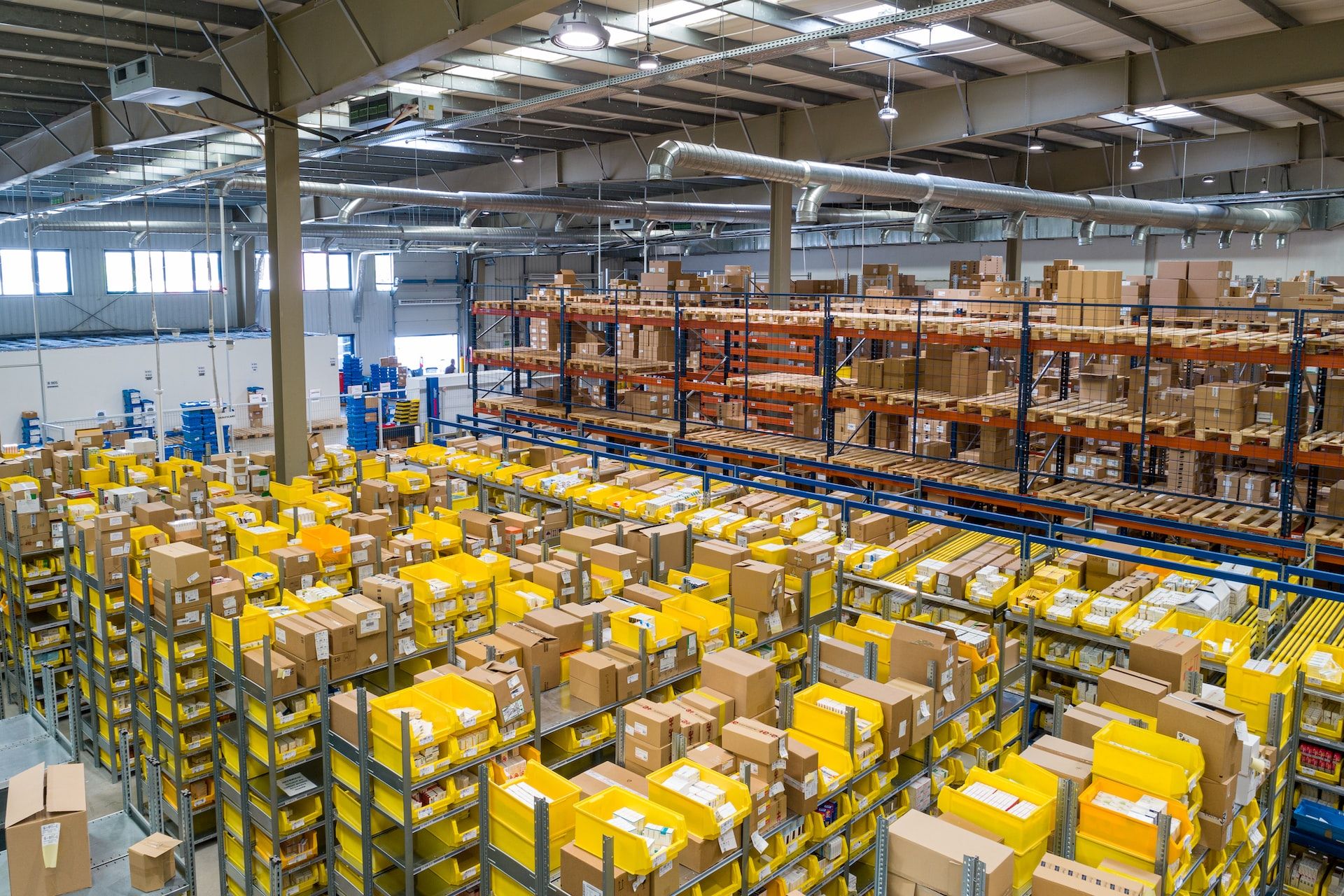
Inventory management is the process of determining the right level of inventory for a business, forecasting future needs, and ordering the proper level of inventory to meet those needs. It is also the process of tracking and accounting for all items in inventory. Inventory management helps businesses keep track of their current stock levels and make informed decisions about when and how to order new items. Inventory management helps in tracking and managing the quantity, quality, and location of goods in order to ensure that they are available when needed and that they are used only when necessary. The goal of inventory management is to ensure the level and availability of product and service , while minimizing cost and waste. Inventory can be tracked in a variety of ways, including counting inventory, manually recording stock levels, or using software to manage inventory.
Elements of inventory management
Inventory management is critical to a business's success since it ensures that there is never too much or too little goods on hand, reducing the danger of stockouts and erroneous records.
The Securities and Exchange Commission (SEC) and the Sarbanes-Oxley (SOX) Act both require public corporations to manage inventories. In order to demonstrate compliance, businesses must document their management procedures.
Inventory management has two key advantages: it guarantees that incoming or open orders are filled and it increases earnings. Management of inventory also includes:
- Cost effective: Knowing stock trends allows you to know how much and where you have something in stock, allowing you to make better use of what you have. This also allows you to keep less stock at each location (store, warehouse), as you can fulfill orders from anywhere — all of this lowers inventory costs and reduces the amount of stock that goes unsold before it becomes obsolete.
- Better cash management: Proper inventory management allows you to spend money on merchandise that sells, allowing cash to flow freely throughout the company.
- Builds customer base : Ensuring that customers receive the things they desire without having to wait is an important part of building loyal customers.
Inventory Management Process
Inventory management process varies between production and business types. For on-demand production, the inventory management process begins when the company receives a customer's order and continues until the order is shipped. Otherwise, the process begins when you anticipate your needs and then order the required raw materials or components. Other parts of the process include analysis of sales trends and organization of product storage in the warehouse.
How Inventory Management Works
The purpose of inventory management is to know how much merchandise is on hand and where it is in the warehouse.The fully automated integrated system tracks the movement of items from the supplier to the consumer via the manufacturing process. Inventory management at the warehouse keeps track of stock receiving, picking, packaging, and shipment.
Different Inventory Management Techniques
Formulas and analysis are used in several inventory management strategies to plan stock. Others rely on standard operating procedures. All of the strategies are designed to increase accuracy. The tactics that a corporation employs are determined by its demands and inventory.By reading the guide on inventory management strategies, you may figure out which strategy is appropriate for your company. Here's a rundown of a few of them and what they're all about:
ABC Evaluation:This approach works by determining which stock kinds are the most and least popular.
Batch tracking: Combines similar goods together to track expiry dates and hunt down problematic items.
Bulk shipments: Unpacked supplies that suppliers load straight into ships or trucks are considered in this manner. It entails purchasing, storing, and delivering merchandise in large quantities.
Consignment Inventory Management: When using consignment inventory management, your company will not pay its supplier until the goods is sold. Until your firm sells the inventory, the supplier maintains ownership.
Cross-docking: This procedure entails unloading things from a supply truck straight onto a delivery truck. Warehousing is virtually done away with.
Demand Forecasting: Demand forecasting is a type of predictive analytics that aids in predicting client demand.
Dropshipping: When a supplier uses dropshipping, the client receives things straight from the supplier's warehouse.
Economic Acquire Quantity (EOQ): This formula determines how much inventory a firm should order in order to save money on storage and other expenses.
However, sometimes inventory management can seem confusing with related disciplines. Inventory management is in charge of a company's whole stock. Supply chain management oversees the whole process, from the supplier to the client. Inventory control includes warehouse management, which focuses on goods at a single place.
For example;
Difference between:
Inventory Management and Inventory Control
Inventory management is the process of maintaining an accurate and up-to-date inventory of the assets, products or materials used by a business. Inventory control is the practice of managing inventory to ensure that it meets predetermined requirements and remains within predetermined limits.
Inventory Management and Inventory Optimization
Inventory management is the process of monitoring and managing the amount of inventory that a business has on hand. Inventory optimization, on the other hand, is a practice designed to reduce the amount of inventory that a business has on hand while still meeting customer demand. In order to achieve inventory optimization, businesses must first understand their current inventory levels and how they compare to competitor levels. Afterwards, they can use mathematical models and software programs to identify where they could reduce their inventory levels.
Choosing the perfect software
Now, to attain the inventory management goals of your company, the first step is to choose the perfect integrated solution that can provide your company with all the necessary support it needs. All of these benefits can only be secured for your organization if you utilize the right inventory management software. Nuport's inventory management software provides an integrated and traditional solution for your company's inventory management. Your business may attain its full potential with the help of Nuport's inventory optimization system's expert features. Nuport's software is designed to provide your firm the boost in performance it needs to stay ahead of the competition. Schedule for your demo today!